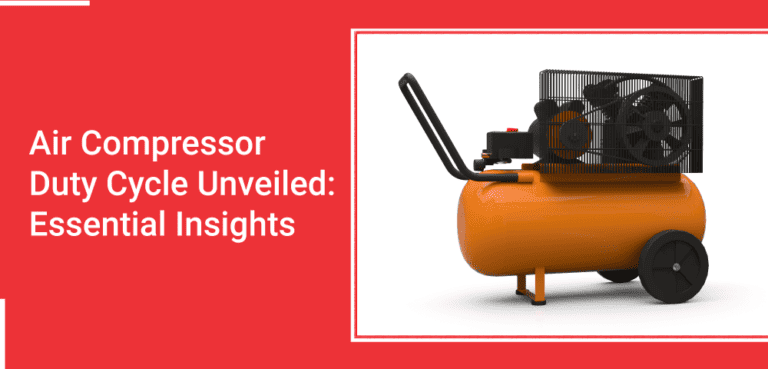
The air compressor duty cycle can be better understood as the frequency at which the machine can be run for a specific time period. For instance, if the air compressor is operating with a 100% duty cycle, it implies that you can run the machine without any need to let it cool down or rest at any time.Â
The industrial air compressor duty cycle is mostly recorded between 50% to 100%, irrespective of the brand or type. For you to better understand the functions of the air compressor cycle and how it determines the machine’s efficiency, read along this article till the end.
A] What is the Air Compressor Duty Cycle?
Remember, it might be easy to understand the air compressor duty cycles, but it might be difficult to actually measure them. This is because there are no universal characters for representing specific values.Â
So, for you to better understand, the air compressor duty cycle is the total time span for which the machine will be delivering pressurised air to meet your industrial applications. If you want to specify it as a percentage, you can calculate the duty cycle by dividing the total run time of the compressor by its cycle time.Â
Depending on your calculation, you might determine the duty cycle of your air compressor to be either 25%, 30%, 50%, 75% or 100%. These are the uniform figures you can assume based on the nearest accurate calculation you attain. It helps you determine the potential run time of your air compressor against the total cycle time.Â
Learning this would help you derive better productivity from your air compressors for diverse applications.
B] Understanding Compressor Duty Cycle Basics
In short, the duty cycle explains how long an air compressor runs continuously. But, to know more about its importance in determining the optimal performance of the compressor, you must first know its basics.
1. Duty Cycle Overview
The duty cycle helps you be sure of the safe & efficient running of your air compressor. For all the high-end industries with pricey applications or processes, it is advised to buy compressors with 100% duty cycles.Â
The duty cycle is also calculated for an air compressor by comparing it with the CFM (flow of air) and PSI (pressure). Suppose your air compressor is operating with 100% duty cycles and at 130 PSI and 30 CFM. In that case, you can conclude that your air compressor will provide you with 130 PSI and 30 CFM for 100% of the time it is running.
2. Factors Affecting Duty CyclesÂ
Remember, the continuous or 100% continuous duty cycle air compressors are mostly used for powering high-end tools or machinery, which can’t bear downtime. This way, operational costs will be reduced, and work efficiency will be attained. However, there are some factors that might affect the duty cycle adversely.Â
The first factor is the size of the tank! The lower the size of the tank, the lower will be the duty cycle. And the second factor is smaller pressure bands! Small pressure bands will lead to a shorter duty cycle. There are ways to overcome these factors by increasing the tank size or widening the pressure band, but that would demand serious technical or mechanical alterations.
3. Impact on Compressor Lifespan
You must know that the duty cycle of air compressors dictates their longevity. A higher duty cycle means that the compressor will be functioning more intensely for a consistent period of time, which will demand high maintenance efforts. There is a risk that the heat will be generated beyond charts, and you will have to refill lubricants more often.Â
In addition to that, the mechanical parts might also wear out sooner when the air compressors run continuously. It is right to maintain the 100% continuous run air compressor frequently over time, as per the manufacturer’s guidelines, to ensure the system lasts longer than specified. On the other hand, moderate-duty cycle air compressors deliver optimal performance and demand less maintenance to last for a longer time.
C] Utilizing and Monitoring Duty Cycles
Here are a few things that you must do in order to monitor and utilise the air compressor duty cycles to your benefit:
1. Matching Duty Cycles to Tasks
As you know, choosing the right air compressor with optimal duty cycles for specific tasks will help you obtain efficient and safe operations for the machine and the end application.Â
The air compressors with a 25% duty cycle are meant to be used only for the smaller applications, which demand only intermittent air power. For instance, it is ideal mostly for domestic or independent applications.
 For a 30% duty cycle, you can consider your air compressor ideal for handling moderate operations where tools are used frequently but not continuously. It can mostly be used in garages where you need to fasten or unfasten some motor parts every 10 or 20 seconds.Â
50% duty cycle implies the air compressor to be used in medium-scale applications where there is only the need for necessitating intermittent air power. Facilities that do not want to invest in large air compressors can use 50% duty cycle air compressors for most of their applications.Â
The 75% and 100% continuous-duty air compressor is ideal for high-end applications. With a 75% duty cycle, you can consider using the air compressor for pneumatic applications through the use of tools in intervals of seconds. And 100% duty cycle is mostly required in the factory settings where no downtime is expected!
2. Monitoring and Maintenance
You must implement preventative maintenance of your air compressor over time to ensure it performs feasibly with consistent duty cycles as recorded. For you to be able to monitor your air compressor performance with respect to the specified duty cycles, here are a few things you must look out for:
- System’s safety shutdown inspection reports.Â
- Check all the displayed readings.Â
- Look whether the condensate is being discharged during the operation.Â
- Drain the condensate manually when required.Â
- Check the dew point for the air compressors with the integrated dryers.Â
You can take the help of experts to get done with the monitoring over different periods of time. In case any discrepancies are found, get the compressor maintained to retain its optimal duty cycles and performance efficiency.
3. Avoiding Overworking
Considering the duty cycle of the air compressor, you must utilise the machine for only a specified amount of time. After that, you must shut it down to allow the compressor motor to cool down before it can be used again.Â
Straining the compressor beyond its capabilities will lead the motor to wear out, the system to overheat, and the compressor to malfunction. So, do give periodic intervals for the compressor to retain its efficiency.Â
D] Duty Cycles and Performance
Here is a clear elaboration on how duty cycles align with the performance quotient of your air compressors:
1. Efficiency and Performance Impact
With a 100% duty cycle, the air compressor will be able to provide you with the rated CFM for a consistent period of time, may it be ten minutes, 30 minutes or a couple of hours, before it demands a cool down. If the air compressor comes with a built-in system for cooling, you can expect it to deliver even higher performance with longer running times.Â
Some of the air compressors come with a pressure lubrication facility for facilitating better cooling. The compressors that come with shorter duty cycles, such as 25%, 50%, or 75%, have their specific rest time embedded into the running cycle. Thus, the efficiency and performance of the air compressors vary depending on the duty cycles.Â
2. Temperature and Duty Cycles
The intermittent duty cycle air compressor requires proper cool off and cycle down period for the machine to prevent overheating. This way, you can prevent the air compressor from experiencing serious wear & tear over the machine. Most of the piston air compressors are ideal for intermittent duties, even though they come with a 100% duty cycle.Â
If the compressors are running consistently without enough time to rest down between the time period when the machine is making pressurised air, it will trigger overheating. It is the situation that will occur when pressurised air is being used faster than the rate at which the air compressor can cope with its usual duty cycle.
Conclusion
This article gives you a clear insight into the air compressor duty cycles and how it is important for improving the performance of your industrial applications. For high-end industrial applications that require pressurised air, you must look out for a 100% duty cycle compressor, and for smaller applications, you can count on 25%, 30%, or 50%.Â
You must not just consider the duty cycles but also tend to utilise them in the optimal manner. If you have been looking for the best quality compressor with optimal duty cycles, Bimpex Machines Pvt Ltd. is the best air compressor supplier that provides you with the best options for satisfying your industrial applications. Contact us today, and let’s discuss your requirements today!