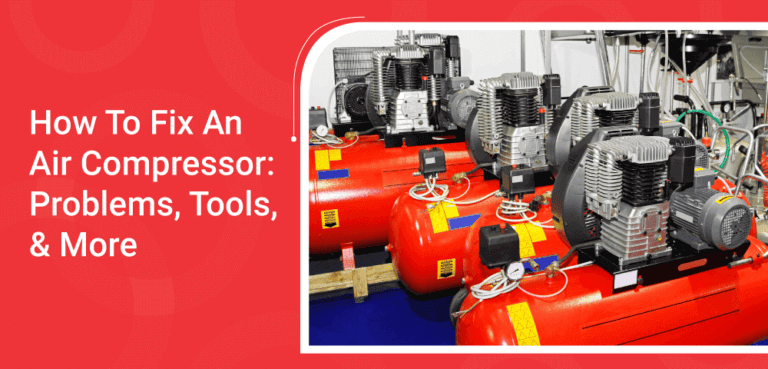
Whether it is household or workshop, air compressors are an essential part of pressure systems applications to ensure their optimal performance. Since it is mechanical equipment, it can potentially malfunction after frequent use. The compressor may leak, or there could be faulty pressure switches. Sometimes, air compressors might not function accurately to supply clean, high-pressure air to other devices.Â
Hence, it’s crucial to guarantee these devices function well with proper diagnosis and repair. You can count on some DIY tricks for air compressor fixes. It not only saves you time on calling and waiting for professionals to get done with the repair but also saves you money. It will make you confident to maintain and troubleshoot these equipment with your own skills using the right tools and knowledge. Read this guide to get in-depth knowledge on air compressor issues and how you can fix them.
A] Common Issues With Air Compressors
There are various industries that depend on industrial air compressors to supply continuous compressed air. However, without it, you can face various issues that can cause downtime. Here are some common issues for diagnosis and resolving air compressor issues effectively:
1. Air Leaks
Air leakage is a common and tough issue to fix which mostly occurs in the tanks, hoses, and fittings. When the compressor gets old, the valves can wear out to gradually loosen the connections, leading to a pressure drop. If the gauge indicates low pressure after deactivating the air compressor while the tank is full, you will know that there is a leak.
2. Starting Failure
There are several reasons why air compressors could experience starting Failure. Examine the power connection and settings, make sure the power cable and switch are connected appropriately, and check the power connection to find out the underlying problem. Furthermore, if there is a deficiency of oil, it can cause the compressor to malfunction. Therefore, make sure to change the fluids on a regular basis and keep the oil compartments filled. If you want to learn how to repair an air compressor for starting Failure, adjust the pressure set points accordingly to prevent frequent turning off and turning on.
3. Shut Down Failure
When the tank pressure hits the cut-out point, air compressors often fail to turn off. If the compressor loses the ability to properly shut down due to a faulty valve, it can cause serious harm. Therefore, it’s essential to quickly replace the power switch and valve when the compressor fails.
4. Bogged Down Issues
It can be the motor part causing the bogged-down issue. If the components are old or there is low lubrication, this issue can occur. If you want to know how to fix a compressor, make sure to change oil and replace components frequently. It will reduce bog-down issues to not hamper the equipment capacity and keep it suitable for your application.
5. Flow Issues
Having clogged filters or any valve with low airflow can reduce the compressor’s efficiency. If you see any of these components are damaged, replace them with new ones. When the pressure gauge setting is low, the coupler is not the right fit for the compressor, or if there is any obstruction straining the equipment, it indicates airflow issues.
6. Strange Noise And Vibration
If you hear any loud noise or vibration coming from the compressor, there can be an issue with the bolts or motors. The pulleys can be misaligned, or any part is loose to cause the noise. Perform routine visual and sound inspections, tighten loose bolts, and replace broken parts to reduce noises and vibration issues.
7. Oil ProblemsÂ
Compression performance can be affected by oil-related issues, such as low oil levels or polluted oil. If you are DIY fixing it, follow the manufacturer’s recommendations for oil changes and do routine checks of the oil’s quality and level. This keeps internal components from any harm and ensures adequate lubrication.
8. Extreme Heating
If overheating is not quickly handled, it might result in serious consequences. In order to combat air compressor overheating, make sure the cooling fan is operating properly. Make sure to maintain clean cooling fins and check for adequate ventilation.Â
9. Lack Of Air Pressure
When there are leaks in the system, and the compressor has a faulty pressure switch and regulator, they can all contribute to insufficient air pressure. Make sure to check and modify the pressure settings and fix the regulators and leaks to maintain ideal air pressure.
B] Tools You Need To Fix Air Compressor
Buy the bellow tools to learn how to fix an air compressor:
- Needle Nose Pliers: These pliers are crucial for precisely grasping and manipulating small parts, such as wires and seals, during repairs and complex pieces.
- Adjustable Wrench: You can use an adjustable wrench for securing more than one type of bolt that is of different sizes.
- Wire Cutters: While working with electrical components or fixing broken wires, wire cutters are essential equipment for precisely preparing wires.
- Screws: It’s helpful to have a range of screws on hand when changing or fastening different parts while learning how to repair air compressors since it ensures that the right type and size of screws are accessible for fixing.
- Screwdriver: A screwdriver is a vital instrument for taking out or putting in screws. You can find different varieties. But most air compressors require flathead and Phillips variety for removing and assembling parts.
- Bolts: Just like screws, bolts come in a variety of sizes you can use to replace and secure parts in the compressor. They are the ideal fastening solution, whether it is a household or industrial air compressor.
C] How To Repair Air Compressor?
You must find out the issues before starting the repair process. Here are some common DIY processes for air compressor repairs:
1. Repair Leaks
- Step-1: Start with unplugging every adjoining tool and hose to operate the air compressor that allows the pressure to build
- Step 2: Apply a soapy water solution around every fitting after the unit is pressurised properly. Any leakage around the fittings will form bubbles.Â
- Step 3: Depressurize the compressor to fix the leakage fittings using Teflon tapes and repeat the whole process to ensure there are no more leakages.
2. Adjust Airflow
- Step-1: Adjust the screws below the pressure-maintaining valve and turn off the top and bottom screws before turning on.Â
- Step-2: Now use an extra upper screw to adjust the airflow while turning on and off the compressor to control pressure.Â
- Step-3: Tighten or loosen the upper screw to adjust the airflow and ensure ideal pressure.
3. Replace the Unloader Valve
- Step-1: If there is a flaw in the unloader valve in the compressor, it requires replacing a part; rather than repairing it, replace the part for optimal performance.Â
- Step 2: The faulty valve can trap air over the piston and hinder the airflow. So, inspect it and clean it before replacing it with the new part if the issue persists.
4. Compressor shut down
- Step-1: Check for any malfunction in the pressure switch and motor. Moreover, check if the filters are clogged to fix the air compressor overheating.Â
- Step 2: Clean the filters or replace them to ensure proper ventilation.Â
- Step 3: If the issue persists, replace the pressure switch.
5. Repairing Electrical issues
- Step-1: If the fuses and breakers pose persistent issues, replace the extensions with direct connections to the power source.Â
- Step 2: Check for any old motor that induces electrical issues from blow fuses and breakers. Replace them to reduce electrical issues.
6. Replacing the broken filters
- Step 1: It’s best to replace the broken intake filters that are essential to the entire unit. They are more prone to damage as the intake filters come out from the compressor.Â
- Step 2: Make sure to find filters with similar thread, portal sizes, and appropriate diameters from the air compressor supplier to replace the intake filters.
D] Know When To Repair And When To Replace
It can be helpful to learn when your air compressor needs repairing or replacement to maintain its efficiency. Make sure to identify the faulty components to determine the issues.
When checking whether to repair worn-out or damaged essential components, keep an eye out for faulty indicators. If the compressor is showing decreased efficiency due to frequent component breakdowns or old, worn-out components, then it’s best to replace them. But if any issues can be solved with a simple DIY process, repair them to boost the equipment efficiency.
Check the manufacturer’s instructions and specifications to locate the appropriate replacement components for your air compressor. Reputable providers frequently offer detailed compatibility information for DIY compressor fixing. It will prevent damage and improve air compressor performance.
Conclusion
An air compressor is one of the most integral systems being used across diverse industries, as it powers most of the pneumatic tools for streamlined all-round operations. Overheating is one of the major issues that might deteriorate operational efficiency and lead to expensive repairs in the long run.Â
Therefore, it is important for all industries using air compressors to implement some preventative measures to repel overheating issues. Bimpex Machines Pvt Ltd. brings you the best quality air compressors and will suggest the right maintenance efforts to ensure excessively hot air compressor issues don’t persist. Contact us to know more!