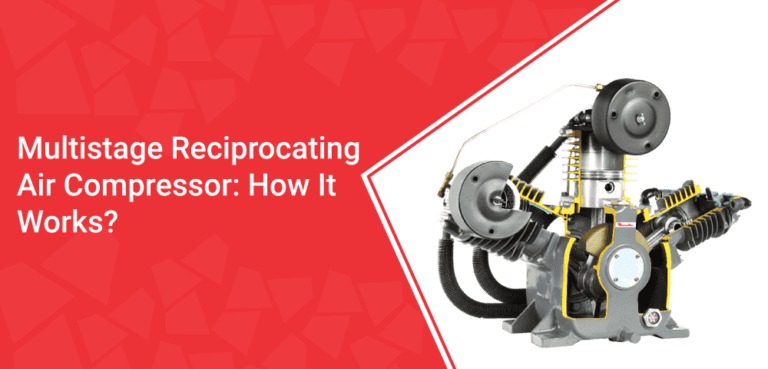
A reciprocating air compressor makes use of piston crankshafts, which are responsible for pressurising air. As a result, the density of air will be increased while the volume will be decreased. With such compression, the air can be easily stored, transported, and utilised effectively.Â
The use of multi-stage reciprocating air compressors enables industries to generate higher pressure volumes at medium-to-high capacities for feasibly executing high-end industrial applications. This helps industries scale their operational efficiency and reduce overhead expenses.Â
If you intend to learn more about the working process of multistage reciprocating air compressors, read this article till the end.
A] Components of Multistage Reciprocating Air Compressors
The major components of the multistage reciprocating air compressors include:
Frame
It is the rugged housing that consists of all the rotating parts over which the crosshead and cylinder guide are mounted.Â
Cylinder
It is the pressure vessel that holds the air in its compression cycle. The multistage reciprocating industrial air compressors consist of two or more cylinders to serve the industrial applications.
Distance Piece
A distance piece brings you a separation between the frame and cylinders, which is integrated either as a single or double-compartment unit.Â
Crankshaft
The crankshaft is the rotating part of the multistage reciprocating air compressor, which moves around the axis of the frame and drives motion to the piston rod, piston, and connecting rod.
Piston and Bearings
The piston is placed at the extreme end of the piston rod and is referred to as the movable barrier within the cylinders. On the other hand, bearings are installed all around the frame of the compressor to ensure better axial and radial positioning of all components.
Valves
The compressor valves are meant to permit the flow of air in a desired direction or to block its flow in unwanted directions.Â
If you are looking to expand your knowledge about the components of an air compressor, you can refer to our comprehensive guide to air compressor parts.
B] What Are The Key Working Principles
A multistage reciprocating air compressor is available in either two-stage or three-stage units. Moreover, they are also categorised with respect to rotary screw or piston-style units. But as far as the working principle is concerned, it is the same for both types of multistage compressors, which is:
- In the first stage, the atmospheric air will flow into the compressor’s air end and will complete a full compression cycle through the rotors or pistons.
 - This air will then be passed through the intercooler for executing the cooling stage. Here, the moisture is allowed to drain out or dry away, which prevents overheating of the system.
 - The cooled and compressed air will then move onto the next stage where another set of rotors or pistons await for giving a second round of compression to the already-compressed air.
 - If there are any more cylinders or stages integrated into the multistage reciprocating air compressor, then the same process will keep on repeating itself until the output end is reached.
Â
With every compressor stage, the air will be further squeezed into a smaller space, which will increase the pressure. The multistage air compressor has the proficiency to obtain a higher PSI than that of the single-stage air compressor.Â
C] Applications of A Multi-stage Reciprocating Air Compressor
The use of a multistage reciprocating air compressor is required mostly in industries that have the production demand for compressed air in high volume but at medium pressure. For instance, the pharmaceutical and automotive industry demand the use of such air compressors. Some of the applications to give you clarity on the usage of multistage reciprocating air compressors are:
Temperature Control
Multi-stage air compressors are used for controlling the air temperature more efficiently than any of the other types of compressors. Here, the atmospheric air will be cooled down before it enters any chamber, which shall result in lowering the output temperature of the air.Â
High-Pressure Applications
If your industrial applications require high pressure, an industrial multistage compressor is considered an ideal choice, which can produce up to 90PSI at the first stage and scale up to 175PSI in the second stage. It is meant for handling high-end industrial applications that demand a maximum pressure of up to 6000PSI.
Oil-Free Applications
The high-end applications often require oil-free air compression, for which the multistage system is an ideal pick. It doesn’t use oil as its coolant but has an intercooler that does the job. The purpose of an intercooler is to reduce the temperature within the stages and eliminate moisture through condensate management.
D] Benefits Of Multi-Stage Air Compressor
Some of the benefits associated with using the multistage air compressors include:
Astounding Energy Efficiency
Multistage air compressors are more efficient in terms of energy utilisation than that of the single-stage counterparts. When there are two or more compression stages, the machine doesn’t have to work too hard to generate a similar amount of pressure. Thus, the energy bills are lowered.
Lowered Moisture
Multistage air compressors operate oil-free, for which an intercooler is used within for acting as the air-dryer. As a result, the air cools down, and the moisture is dried or removed completely through the attached drain. Thus, less strain is imposed on the filters or dryers.
Low Overheating Issues
Intercoolers being used in the multistage reciprocating compressor also reduce the risk of overheating scenarios by eliminating some amount of heat during the dual-stage compression. Thus, it means that the compressor will run cooler while making the air.
Enhanced Reliability
Lowered heat and enhanced efficiency are what ensure your system will experience less wear & tear, mostly around the seals and motors of the compressor. Over time, this will lead to lowered downtime and fewer maintenance halts, ensuring high reliability.
Size-per-CFM is Small
Considering the size, the multistage reciprocating compressor is meant to deliver high pressure and more CFM or air compared to the single-stage compressor of the same size.
E] Multistage Reciprocating Air Compressor Vs. Single Stage
Some of the potential differences between single-stage and multistage air compressors include:
- Single stage compressor comes with just one cylinder for handling the compression process, whereas more than one cylinder is connected in series, while you use the multistage option.
 - A multistage air compressor, mainly three-stage, is required mostly for high-pressure ratio applications, whereas a single-stage compressor is meant just for low-pressure applications.
 - In a single-stage compressor, the cylinder size is quite big in comparison to that of the multistage reciprocating compressor.
 - No adequate temperature control is embedded in the single-stage air compressors, whereas the intercooling technology of multistage compressors tends to lower the temperature within compression stages.
 - Lubricating oil is burnt in more quantity in single-stage compressors, whereas effective and long-lasting lubrication is attained with the multistage option.
 - The rate of leakage loss is higher for the single-stage compressors than that of the multistage compressors. In fact, the chance of any form of leakage is less with the robust frame and structuring of the multistage air compressor units.
 - Single stage air compressors often experience high-torque fluctuations, due to which they require a larger flywheel. On the other hand, multistage air compressors generate uniform torque, which works fine with smaller flywheels.
Conclusion
Now, you might have clarity on the efficacies of multistage reciprocating air compressors, and how they are better than that of the single-stage compressors for high-end industrial applications. The multistage compressors can deliver high amounts of CFM in the air to support applications in oil & gas, pharmaceutical, automotive, and other such industries.
Not only that, but the natural gas industry also utilises the same set of compressors for transporting gas through various cross-country pipelines.Â
This expresses the importance of multistage reciprocating air compressors in the modern industrial world. If you have an industrial setup and are in need of a compressor that projects utmost efficiency, contact us right away!