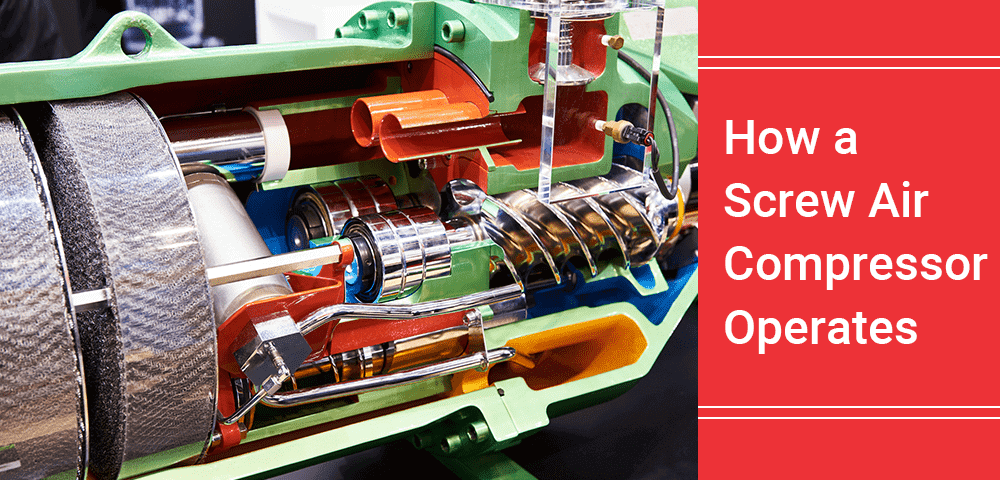
Rotary Screw Air Compressors are one of the most widely used types of equipment among modern industrial machinery. These air compressors are renowned for their overall versatility and reliability and act as the ultimate powerhouse behind a wide range of industrial applications and processes. The highly durable technology is well-suited for a wide array of challenging industrial tasks. This is why understanding how these air compressors work is of utmost importance.
A] What are screw Air Compressors?
Before you understand the working of screw air compressors, it is imperative to know what it means and why it is important. Rotary screw air compressors are known to make use of a specific rotary positive displacement mechanism consisting of screws or helical gears for compressing air by minimizing the chamber’s pressure. The overall mode of operation or working principle of screw compressor appears somewhat similar to that of centrifugal compressors or reciprocating pistons.
The primary difference between centrifugal or reciprocating compressors and rotary screw air compressors is that the latter helps in delivering a non-pulsating or constant stream of compressed air while being 100 percent duty cycle devices.
B] Types of Rotary Screw Air Compressors
Before we get an insight into the rotary screw air compressor working principle, let us understand its standard types:
Â
1. Lubricated Screw Compressors
These variants of air compressors will feature improved durability, reliability, and maximum efficiency. Due to the presence of these high-end characteristics, rotary oil compressors are regarded as the best choice for a wide range of manufacturing processes. These compressors are, therefore, utilized across the world throughout different industries.
The oil-based screw air compressor is regarded as the best choice for applications requiring medium air pressure. Therefore, it is best-suited for applications requiring huge amounts of medium air pressure. In the given type of compressors, oil is injected into the respective compression chamber for ensuring compression. The injected oil helps in lubricating and decreasing the temperature of the respective compressor components. The oil also helps in assisting the compressor in reducing the chamber leakage while eliminating heat during the process of compression.
The oil-lubricated compressor can continue working the entire day without delivering any negative effects. Therefore, these are best-suited across manufacturing applications wherein a stopped compressor might affect the overall production. The oil-lubricated air compressors are also recommended for applications wherein air demands tend to be tough to analyze or wherein you cannot control the overall demand.
The compression chamber is responsible for controlling the temperature of injected oil from around 60 Degree C to 700 Degree C. The outlet oil temperature is expected to be kept above the pressure dew point for minimizing condensation of water mixing with oil. The thermostatic valve is responsible for controlling the total amount of oil circulating in the bypass line or the air cooler. It helps in maintaining the overall temperature within a wide spectrum of ambient temperatures.
2. Oil-free Screw Air Compressors
This type of rotary screw air compressor does not make use of any oil during the process of air compression. These compressors are known to make use of lubricants for minimizing the overall motor temperature while eliminating heat by the respective motor. In some of these oil-free compressors, even water is used as the lubricant.
The oil-free compressor does not make use of oil at all in its compression chamber. The compressor is helpful in efficiently eliminating the overall risks of contamination from the compression chamber due to the absence of any oil. The oil-free air compressor is regarded as the best choice when you are concerned about air purity for the products. It is because even minor impurities are capable of spoiling the process and damaging the end product. This is the reason why most manufacturing companies make use of oil-free screw compressors to make the overall air free from any contamination.
Oil-free screw air compressors are typically used in sensitive industrial applications. As these industries are expected to meet strict standards for beverages, food, and pharmaceuticals, these need the utilization of oil-free air compressors.
Here we have covered two types of rotary screw air compressor, you can explore more types with our guide: Air Compressors: Types, Uses & Factors To Consider Before Buying.
C] Elements in the Screw Air Compressor
1. Male & Female Rotors
The rotors usually depict the shape of the helical screw. There is the presence of a male rotor & a female rotor. The thick part is the male rotor featuring dedicated lobes. On the other hand, female rotors are thin components featuring flutes or grooves. Air is trapped between both male & female rotors. Eventually, it is transported to the exhaust part of the element within air pockets. These are pockets of air trapped between male & female rotors. Typically, a male rotor will feature 4 lobes. At the same time, the female rotor will have 6 grooves.2. Airend Assembly
The screw element or air-ends of the rotary screw air compressor are the most significant parts of the entire module. Air-end assembly serves to be the part of the machine wherein actual air compression occurs. It is regarded as the heart of any rotary screw air compressor. Air-ends usually feature constant flow or volume along with variable pressure. This implies that at a given speed or rpm, they will always be supplying the same volume of air. Still, it can be achieved in varying pressures. As the entire process is continuous, the elements are helpful in supplying a non-pulsating, steady flow of air with minimal maintenance & vibrations and maximum lifespan.D] How Does a Screw Compressor Operate?
1. The Air Circuit
In this mechanism, air is drawn through the open inlet valve and the filter. It is passed to the compressor element while getting compressed there. A mix of oil and compressed air is flown into the oil separator or air receiver through a check valve. Eventually, air gets discharged through an outlet valve with the help of a minimum pressure valve & the air cooler. In case of loaded operation, a minimum pressure valve helps in keeping the pressure in the respective separator tank above some minimum value, essential for lubrication. The presence of an integrated check valve helps in preventing the compressed air to go downstream and vent into the atmosphere in case of unloaded operation. As the compressor is stopped, the inlet valve and check valve will eventually close. This will prevent compressed air from venting into the air filter.2. The Oil Circuit
In the oil separator or air receiver, a significant amount of oil is separated from the air-oil mixture through some centrifugal action. The remaining oil gets removed with the help of the oil separator. The oil gets collected at the bottom part of the air receiver or oil separator, serving the role of an oil tank. The entire oil system is supported by the presence of the thermostatic bypass valve. As the oil temperature reaches below a specific point, the bypass valve will eventually shut off the supply to the respective oil cooler. Therefore, the oil cooler is bypassed. Air pressure will ultimately force the oil from the oil separator or oil receiver through the oil stop valve and oil filter into the module’s compressed chamber. The bypass valve will start the supply from the cooler as the oil temperature increases to the specified point. At around 15 Degree Celsius above the specified point, all the oil will eventually flow through the oil cooler. The oil stop valve will prevent the compressor element from getting flooded with oil as the compressor will stop.E] Conclusion
Rotary screw air compressors are regarded as one of the most energy-efficient variants of air compressors. They also tend to be more compact, making them ideal for applications within smaller spaces. Rotary screw compressors can help in delivering a wide range of benefits to different industrial applications, including:
Quiet operation in comparison to other types of air compressors