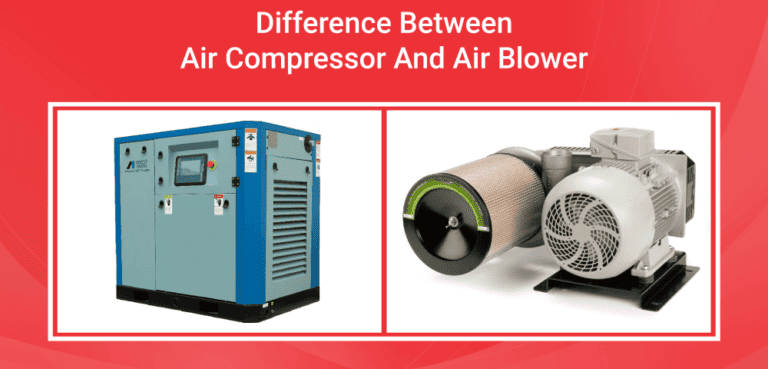
In industrial applications, pneumatic systems play a very major role in providing operational benefits. For every fabrication or assembly application that demands high speed, accuracy, and force, pneumatic systems are the forefront necessities.Â
Blowers and compressors are inevitable parts of a pneumatic system, as they operate at low-pressure and high-pressure ratios, respectively. The compressors function in a way such that they compact the air into tiny spaces by making it denser and more pressurised. On the other hand, the blowers move the air with a subtle rise in the pressure when needed.Â
A lot of you might not be aware of the application difference between a blower and a compressor while using a pneumatic system in your industrial setup. So, this article is going to help you with the difference between an air blower and a compressor.
A] What Are Industrial Air Blowers?
An industrial air blower, one of the important components in a pneumatic system, serves the major function of supplying heavy gas or air flow to diverse industrial processes. The construction of these components includes electric fans with blades and wheels, which the component then uses to drive the air current from source to destination.Â
Industrial class blowers have been used as crucial equipment for diverse work purposes and for adding the utmost efficiencies. As far as the functionality aspects are concerned, industrial blowers offer ventilation, combustion, cooling, drying, air-cleaning, and other such functions.
Several industries, such as chemical, oil, automotive, mining, and construction, make use of these industrial blowers for their specific applications. Some of the benefits of using industrial air blowers include:
- The industrial air blowers are efficient in terms of energy consumption, which makes them a cost-effective component.Â
- The air blowers are quite useful and immensely effective for diverse functions, which makes them a versatile consideration for several industries.Â
- It is a self-sufficient equipment or component that doesn’t need human supervision to run.Â
- The construction of air blowers is done in a manner such that they can move large air quantities consistently without the need for any supervision.Â
- Maintenance requirements are low for industrial air blowers when compared to the other systems.
B] What Are Air Compressors?
Industrial air compressors, on the other hand, are more impactful than that of blowers, especially in the industrial setup. It is basically a machine that has the capability of reducing the volume of atmospheric and standard air. And that’s done by packing the air into a very small space. Now, as the air is compressed, it will be stored securely until someone calls in to release it.
The operating efficiency of a compressor is attained by its high pressure-to-volume ratio, which makes it fit for manufacturing applications. This is because manufacturing tasks require intermittent bursts of pressurised air and user-controlled airflow. As you know, there are two classifications associated with air compressors: positive and dynamic displacement.
Positive displacement is the classification of air compressors where the screws or pistons are used to reduce the air volume within the chamber. On the other hand, dynamic displacement is the approach where the air will be accelerated or decelerated within the chamber using the centrifugal force.
Some of the benefits of air compressors in the industrial applications are:
- Adapts to diverse working conditions.Â
- Enables you to use controlled airflow.Â
- Comes with oil and oil-free options.Â
- Provides you with the utmost energy efficiency.
C] Overview Of The Pneumatic Systems In Industries
Now that you know the difference between an air compressor and an air blower, it is time to learn about pneumatics in brief. It is the technology that has been demandingly used in industrial settings, making use of compressed air. Over time, the application of pneumatic systems has extended to robotics, motion control, automation, and much more.
In other words, pneumatic systems are meant for moving raw materials and other things in an industrial setup from one place to another. To help you better understand this system, here are the components that comprise the pneumatic systems:
- The compressor takes charge of compressing the air and delivering the required pressure essential for the work. To make this process efficient, you will need the best quality VSD air compressors for the job.Â
- The air tank is the component where the air is stored at a certain temperature after it is pressurised by the compressor.Â
- Check valves are used on the hose to connect the compressor to the buffer tank to prevent backflow.Â
- Gauges or regulators are essential components that allow you to control the release of pressurised air to pneumatic tracks.Â
- Actuators in pneumatic systems are components that do all the major work, as they are responsible for converting the energy exerted by the pressurised air and turning it around into a mechanical motion to regulate any control element.
Now that you know about the components, let’s shed light on some of the applications of pneumatic systems:
- Packing machinery
- Fabrication tools
- Filling equipment
- Paint spraying tools
- Robotic arms
- Material handling machinery
- Air-powered equipment
D] Common Industrial Applications Of Air Blowers
For every process that requires the flow of air or gas, industrial air blowers are meant to work as effective mechanical devices for charging the combustion engines or ventilating the mines. Apart from that, they can also perform various other high-end tasks. There are different types of industrial air blowers, ideal for serving diverse applications, which include:
- PD or Positive Displacement blowers make use of mechanical means for squeezing the fluid, which will then increase the velocity and pressure.Â
- Centrifugal blowers are embedded with high-speed blades or impellers for imparting air velocity and are commonly used in ventilation systems.Â
- High-speed industrial blowers are designed in a way such that they can be used for pressure boosting or vacuum waste removal.Â
- Regenerative blowers are considered effective for applications that demand a high air volume at lowered pressure rates.
Apart from these applications, some of the other common applications of air blowers in an industrial setup include:
- Cooling
- Dust loading
- Air handling
- Material Handling
- Mining
- Food industry applications
- Cement works
E] Common Industrial Applications Of Air Compressors
For you to get a better insight into the difference between an air compressor and a blower, you must also learn about the efficacies of the compressor system in diverse application setups:
- An air compressor is recommended for use in automobile repair centres or body shops.Â
- Air compressors are used in the Pet Bottling Industry to fill up the bottles and give them shape.
- It is used in electric-powered tools that are light in weight and don’t include batteries or cords. A tube is used for flowing the compressed air in the tool, which produces adequate force for making it work.Â
- Any industrial process that includes woodworking, coating, metal fabrication, construction, painting, and coating will use an air compressor.Â
- Air compressors are widely used in various medical or healthcare equipment such as surgical instruments, X-rays, and oxygen systems.
In terms of industrial applications, the compressed air is used for:
- Automobile manufacturing applications make use of compressed air for building or assembling critical components and moving heavy objects.Â
- The agriculture sector uses compressed air to power various hand tools, from pain sprayers to nail guns.Â
- The food and Beverage industry makes use of pressurised air for freezing, cooling, filling, bottling, and other such applications.
F] Difference Between Blower And Compressor’s Pressure Ratio
Both compressors and blowers are meant to create streams of pressurised air for different types of manufacturing processes. The pressure ratio ratings of both blowers and compressors are meant to define the output derived by dividing output pressure by inlet pressure.
Compressors work with a high-pressure ratio, whereas blowers operate with a low-pressure ratio. That’s because air compressors are meant to pressure the air in a small space, and blowers are meant to move the air with a slight increase in pressure.
Due to this, the performance implications, alongside energy and cost usage, differ with respect to the use of blowers and compressors.
Conclusion
With this, you are now aware of the difference between air blowers and air compressors being used in pneumatic systems. Depending on your respective pneumatic applications, you can consider using either a blower or compressor for your operational efficiency.Â
Irrespective of what you need for your applications, choosing the right quality compressor or blower becomes of utmost importance. Therefore, be assured you look for capacity, maintenance, and efficiency of the equipment or component before buying it.Â
In case you are in search of reliable air compressors, we are here not just to educate you on the compressor and blower difference but also to provide you with the best quality components. Contact us today to know more!